QUALITY MANAGEMENT MADE EASY
By Rob Somers

I am sometimes amazed at the level of understanding of Quality Management in Aviation. In my opinion most people, especially those on the 'front line' (pilots, engineers, cabin attendants, operations officers etc.), see Quality Management as purely auditing.
This concept could not be further from the truth. Let's start by considering the individual's role in the Quality System by looking at a famous quote.
"Quality means doing it right when no one is looking" - Henry Ford.
The emphasis here is on the fact that you will do your job to an expected standard, even in the absence of a supervisor. It also means that you will not take any shortcuts to achieve the expected outcome; a fundamental quality principle.
Ford expected his factories to produce a product to a certain standard. He could not physically watch over every person in the assembly line; he had to find methods to ensure that the car would still be produced according to his design, even when he wasn't there.
These methods are captured in the familiar term "Quality Assurance" and can be simply described as all those processes or systems that are used to ensure a product or service meets the desired outcome. And here our old friend auditing comes into play for the first time. Auditing is just one of these processes that are used to check how well the job is done measured against a certain criteria and to highlight any possible shortcomings.
Time for a practical example. To be able to get an air service license to fly around people in exchange for money, you basically have to promise the Air Service Licensing Council and the Regulator (SACAA) that you will do so in a safe and reliable manner and in accordance with a set criteria; in this case, the SA-CATS and SA-CAR's.
But to ensure that you do what you promised, you need to establish methods inside your AOC, AMO or ATO that can tell you how well you are doing in terms of this set criteria without the CAA having to 'look over your shoulder all the time'. For this, you need a Quality System.
A Quality System basically consists of two components; Quality Assurance and Quality Control. "But what is the difference?" I get asked all the time.
Let's look at Ford again. He built cars. To build a car, several components and assembly processes are needed. To make sure that the right parts are used, properly trained people are doing the assembly and that the assembly process is done correct and on time, quality assurance techniques or tools are used.
Examples include designing objectives to strive for in every department. For instance in the parts procurement division they might have an objective stating "Parts received from suppliers must be entered into the store's inventory within 2 hours of delivery".
Another important Quality Assurance tool is a single quality policy that is communicated to all, easily understood and implemented by all. This creates a single "mind set" for the employees of the company and should be in line with its overall business model. This way, everyone can clearly see in which direction the company is heading.
Once the car is completed, a test drive is needed to ensure that all the brakes, lights, handling etc. are tested and is in fact compliant to the standard set out at the beginning. This process is called Quality Control.
This is basically a big audit on the final product to make sure that the product meets customer expectations.
In an aviation concept where you're flying around people, the quality assurance tools are items like operational control and supervision, training, management of safety, continuous improvement, compliance, internal auditing etc. The quality control aspect is the safety levels of the operation and the satisfaction of the customer. If they fly with you, feel safe and are on time, they are satisfied.
Let's summarise:
Quality can be described as the measure of something.
To be able to measure how safe, compliant and efficient your company is performing, you need a quality system which comprises two components; quality assurance and quality control.
Quality Management comprises the systematic and documented actions needed to ensure quality of product or service.
In commercial aviation, quality management, similar to safety management, is critical. Without it, a company might never be aware of the ever present threats, especially in this high risk environment.
|
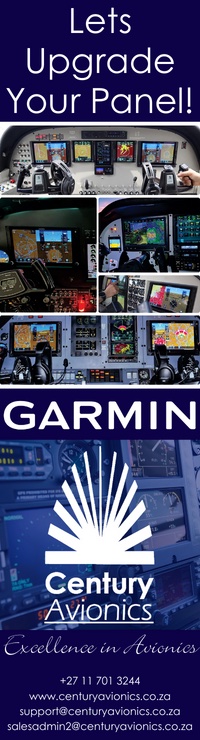  |