TIPS ON ENGINE CARE
By Johan Lottering
To preserve the integrity of engines periods of inactivity must be avoided by regular starts every few days and immediately setting 1000 r.p.m. each time, strictly in accordance with the pilot operating handbook (POH). The book-settings are intended, among other considerations, to avoid brief initial idling periods of the engine running 'dry'.
Engineer Willie Breytenbach explains that Lycoming engines may be especially prone to damage as the cam shaft is situated near the top of the crank case. Oil accumulated in the sump at the bottom through gravity during inactive periods must be scooped up and splashed inside the crank case before metal on metal surfaces, i.e. the moving parts, can be lubricated. At insufficiently low r.p.m. shortly after start the 'splashing' is ineffective for the first critical seconds. Incorrect engine handling technique could steal hundreds of hours from the design-life limit. A particular surface prone to abrasion and excessive wear, if devoid from a protective film of oil is between the cam shaft lobes and the lifters. The lifters are connected via long 'shafts' to rockers which open the inlet and outlet valves in a sequence facilitating ignition timing and combustion. The valves are closed again by spring action. The cam shafts of the Continental engines are situated lower in the crank case, closer to the sump. The cam shaft, being closer to the oil is slightly more resistant to dry running shortly after start as the cam shafts are more readily lubricated at low r.p.m. according to Willie.
Each lifter acquires a unique groove pattern from axial rotation in its position over time. The 'wear imprints' on the lifter heads correspond with each lobe. If the engine is opened for e.g. ultra-sonic shock-load inspection of the crank shaft after a propeller-strike and each part is not restored to its exact former position, problems may later occur. Apart from causing damage to surfaces in direct contact metal, particles in the oil from excessive wear can harm other parts. Bearings can e.g. be excessively worn by metal debris in the oil. On this account care should also be taken to avoid running engines over dirt surfaces with carburetor heat or alternate air open. The sucked in debris can end up in the oil. This is also why air filters must be changed regularly. In the long run foreign particles or debris in the oil can damage a bearing and result in catastrophic engine failure. A damaged big-end bearing can break the conrod driving the piston, in turn breaking the cam shaft and driving the crown through the top. Really!
Shock-cooling of high-performance piston engines has often been blamed for cracked cylinder heads. Some engineers contend that might not be entirely factual, as the aero engine has been designed for sudden vast ambient temperature differences, such as flying through ice and rain.
Cracked areas on cylinder crowns are sometimes found between the spark plug and the inlet valve. This is the area where the temperature difference between the cold incoming fuel-air mixture and the hot ignition is greatest. To alleviate cracks pilots are advised to during descend and approach flight phases with low power settings reduce the richness of the incoming mixture. The correct mixture setting should correspond to 1300 to 1400 degrees Fahrenheit on the Exhaust Gas Temperature (EGT) gauge/s on most Continental and Lycoming engines. This practice will also reduce the risk of engine flooding due to overly rich mixture, especially on short final approach. Care should be taken though that correct procedures for applying power are followed in the right sequence during go-around or missed approach - i.e. mixture/s forward, propeller r.p.m. lever/s forward then throttle/s forward. Fly safely!
|
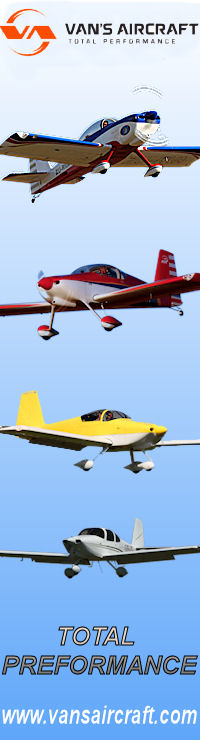 |