New A400M Agreement Strengthens Denel Manufacturing
Denel and Airbus Military have finalised a new agreement with revised terms for manufacturing aircraft components on the A400M, in a development that will contribute significantly to the financial turnaround of the South African company and confirms its position as a top-tier supplier on the world's most advanced military airlifter.
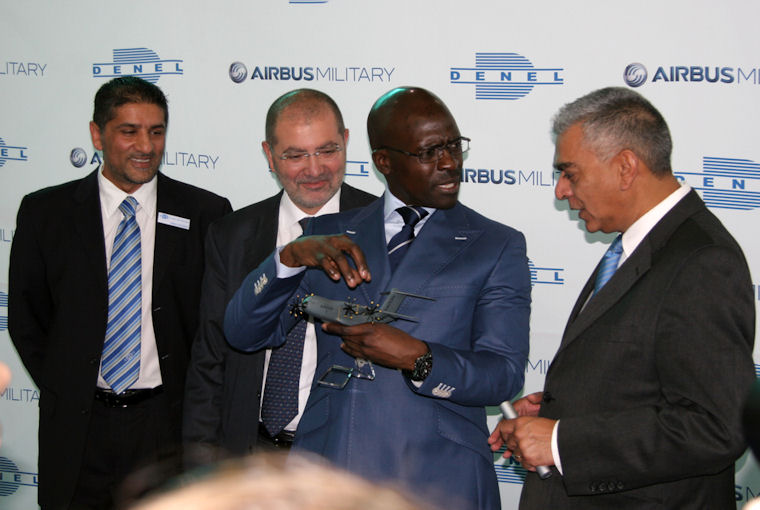
The renegotiated agreement was signed on the 17th of September 2012 at a function in Kempton Park attended by the Minister of Public Enterprises, Malusi Gigaba, the Senior Vice-President of Airbus Military, Mr Antonio Rodriguez-Barberán and the Chairman of the Board of Denel SOC, Mr N R Zoli Kunene.
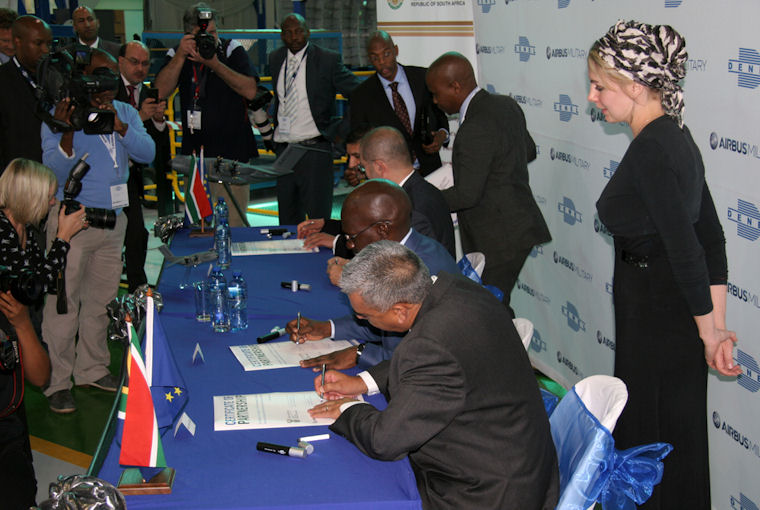
Minister Gigaba said the new agreement demonstrates the confidence of major global aerospace companies in the abilities of the local manufacturing sector. “The relationship between Airbus and Denel takes us another step further towards the growth of a fully-fledged South African aerospace industry,” he said. Riaz Saloojee, the Group Chief Executive of Denel SOC, says the relationship with Airbus positions DAe as an established supplier of high-tech aircraft parts and strengthens South Africa's position in the global aerospace industry.
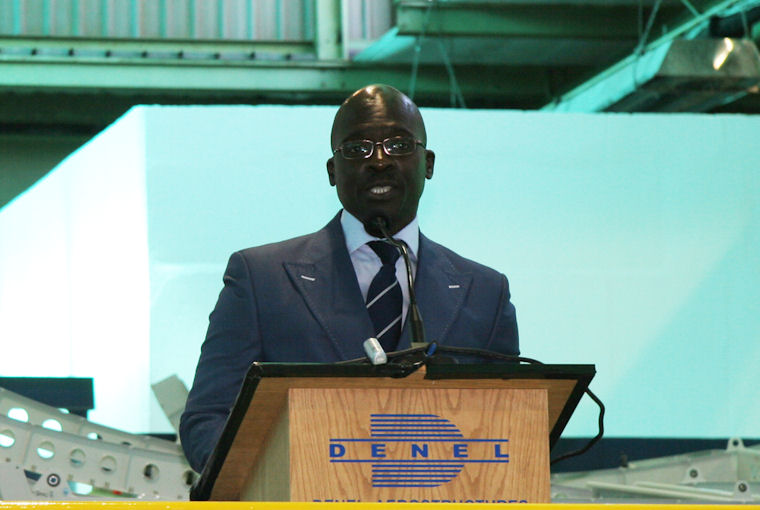
Airbus Military Senior Vice President Commercial, Antonio Rodriguez-Barberan, stated that the agreement “re-affirmed Airbus Military's commitment to South Africa and its industrial partners and suppliers in the country. With series production of the A400M ramping up ahead of the first deliveries next year, it is comforting to know that we have a dependable partner in Denel Aerostructures which can be relied upon to provide top quality work, on-time and within budget”.
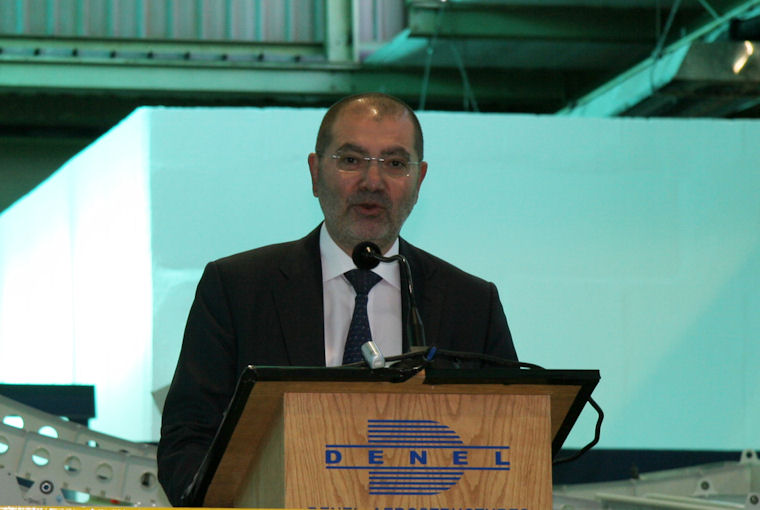
Denel Aerostructures (DAe) manufactures two major work packages on the A400M, the Wing-to-Fuselage Fairing and the Top Shells which form part of the aircraft's mainframe.
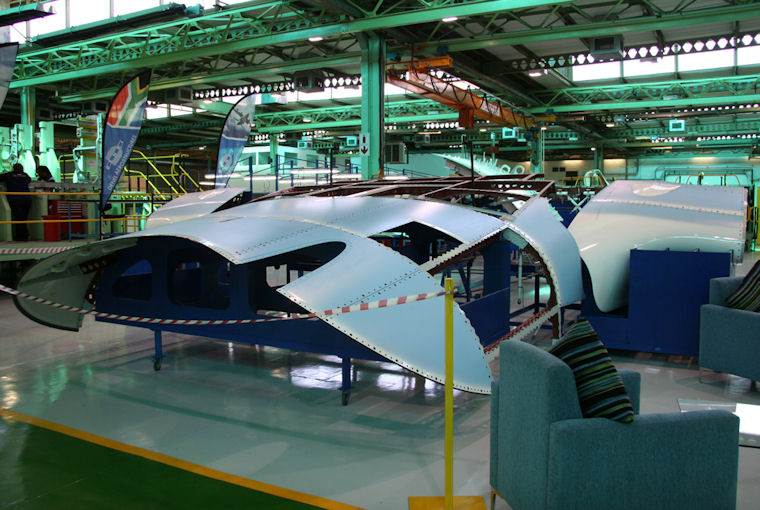
Mr Saloojee says the new agreement together with the restructuring of the company and a strong order pipeline will enable Denel Aerostructures to return to profitability within the next three to four years in line with a turnaround strategy introduced in 2010.
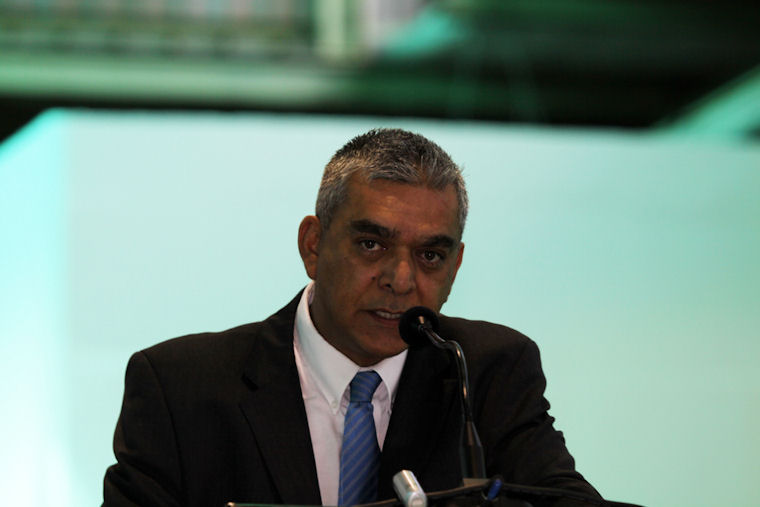
The Government has demonstrated its confidence in the future of the company through a capital injection of R700 million, earlier this year. “This agreement has vindicated this confidence and confirmed the viability and inherent potential of Denel Aerostructures in the years ahead,” he says.
The CEO of Denel Aerostructures, Ismail Dockrat, says the company has already ramped up its production of vital parts for the A400M that will be delivered to customers in the coming months. DAe is one of a select few companies outside of Europe responsible for the design and manufacturing of vital parts on the high-speed turboprop aircraft.
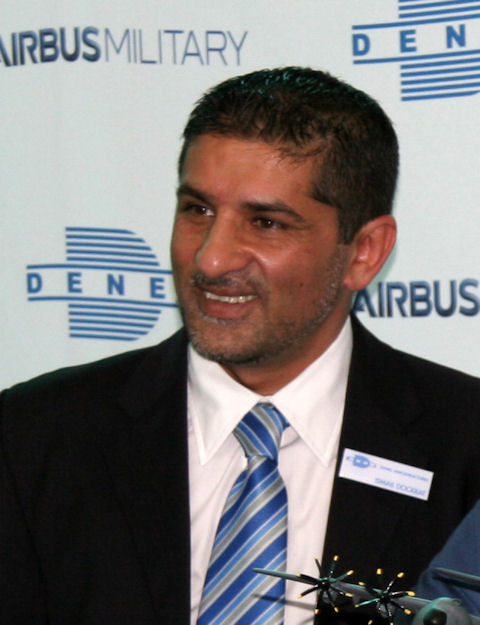
Mr Dockrat says the new agreement will strengthen DAe's capacity to market its products and services to other aircraft manufacturers and to enter into new partnerships for future projects.
Denel's participation in the programme has already brought significant benefits to the local aerospace industry. The new agreement will stabilise local supply chains and give experience to smaller sub-contractors to perform work on a global programme.
Mr Saloojee says the contract with Airbus confirms South Africa's status as a reliable supplier to multinational projects and an innovative design partner.
“It provides DAe with the know-how and capacity to participate in future multinational ventures and to grow the local industry, as envisaged in the recent Defence Review 2012.
“It will strengthen DAe's position in South Africa's aerospace industry and confirms its position as a strategic public asset, its contribution to skills development and advanced manufacturing and it's potential to generate export revenue for the country,” says Mr Saloojee.
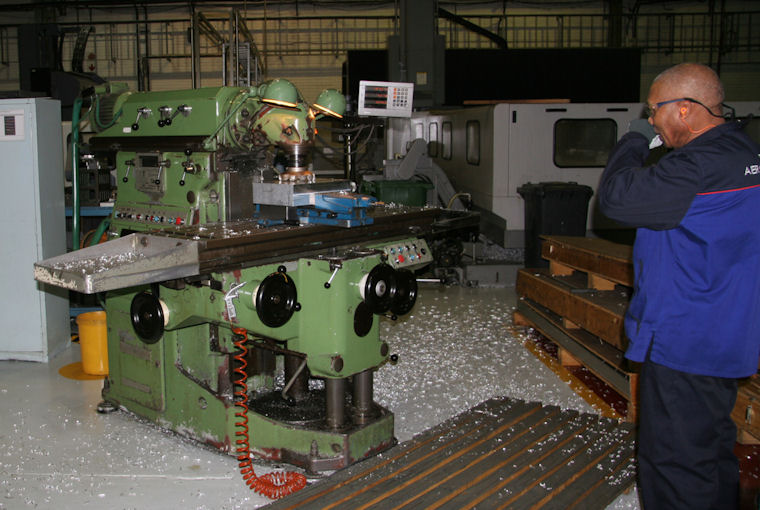
Fact Sheet on Denel Aerostructures' Participation in the A400M Programme:
Located at the Denel campus in Kempton Park, DAe is responsible for the manufacturing of:
· The Wing to Fuselage Fairing -- an essential part of the aircraft that provides protection against lightning strikes, hail damage and bird strikes to the sensitive equipment under the centre wing portion.
· The Top Shells -- made up of more than 1 100 parts consisting of a large machined skin, engineered out of an aluminium alloy. Each aircraft is fitted with two top shells, positioned in front of, and behind the wings where it is joined to the fuselage. The 900 system brackets support the vital electric and electronic wiring, hot air and heat exchange piping and include the aircraft's life-rafts.
All these components have been designed and industrialised at DAe and are manufactured in Kempton Park before being shipped out for final assembly onto the A400M in Seville, Spain. The assembly line in Spain is currently working on the second serial aircraft, to be delivered to the French Air Force in early 2013.
The Chief Executive Officer of Denel Aerostructures, Ismail Dockrat says the detailed and precise testing phase of the versatile airlifter is almost completed and all the suppliers of parts will now be going into serial production mode.
The ramp-up means that Denel Aerostructures will increase production of its parts in the subsequent years. The company is busy consolidating all its operations under one roof in a move that will improve efficiencies and cut costs significantly.
DAe was involved in the A400M from the start and designed the parts from scratch according to the manufacturers' specifications. The manufacturing involves cutting-edge engineering processes including high-speed machining, heat treatment, structural testing and stress analysis.
Mr Dockrat says the company's involvement in the manufacturing of one of the world's most sophisticated aircraft is “a vote of confidence in the quality of local engineering and the skills of the work force.”
|
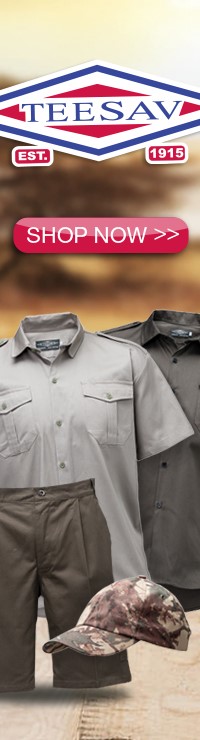 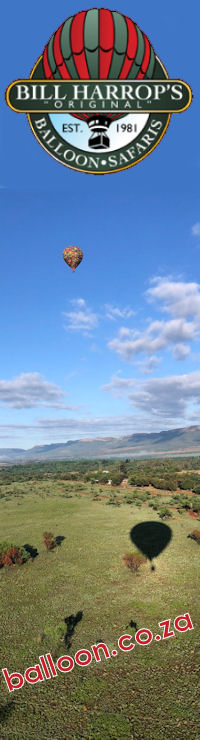 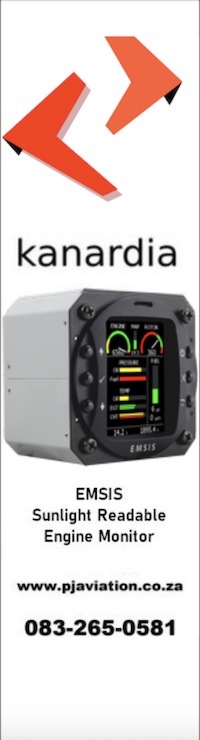  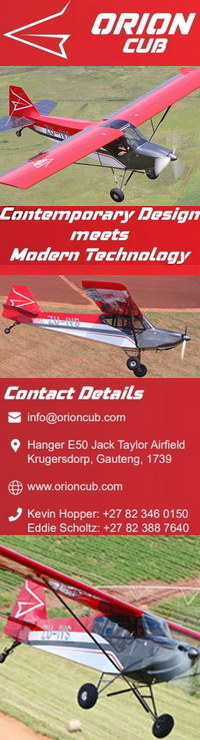 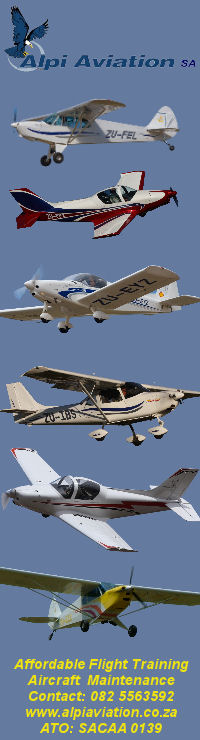 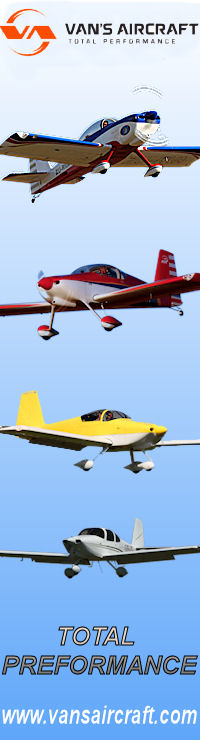 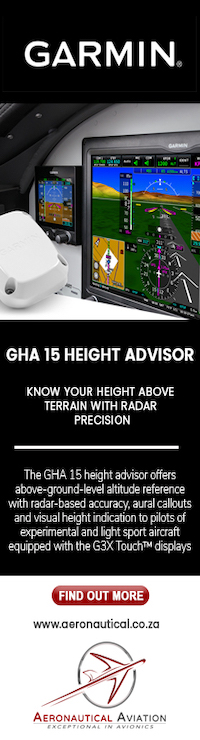 |